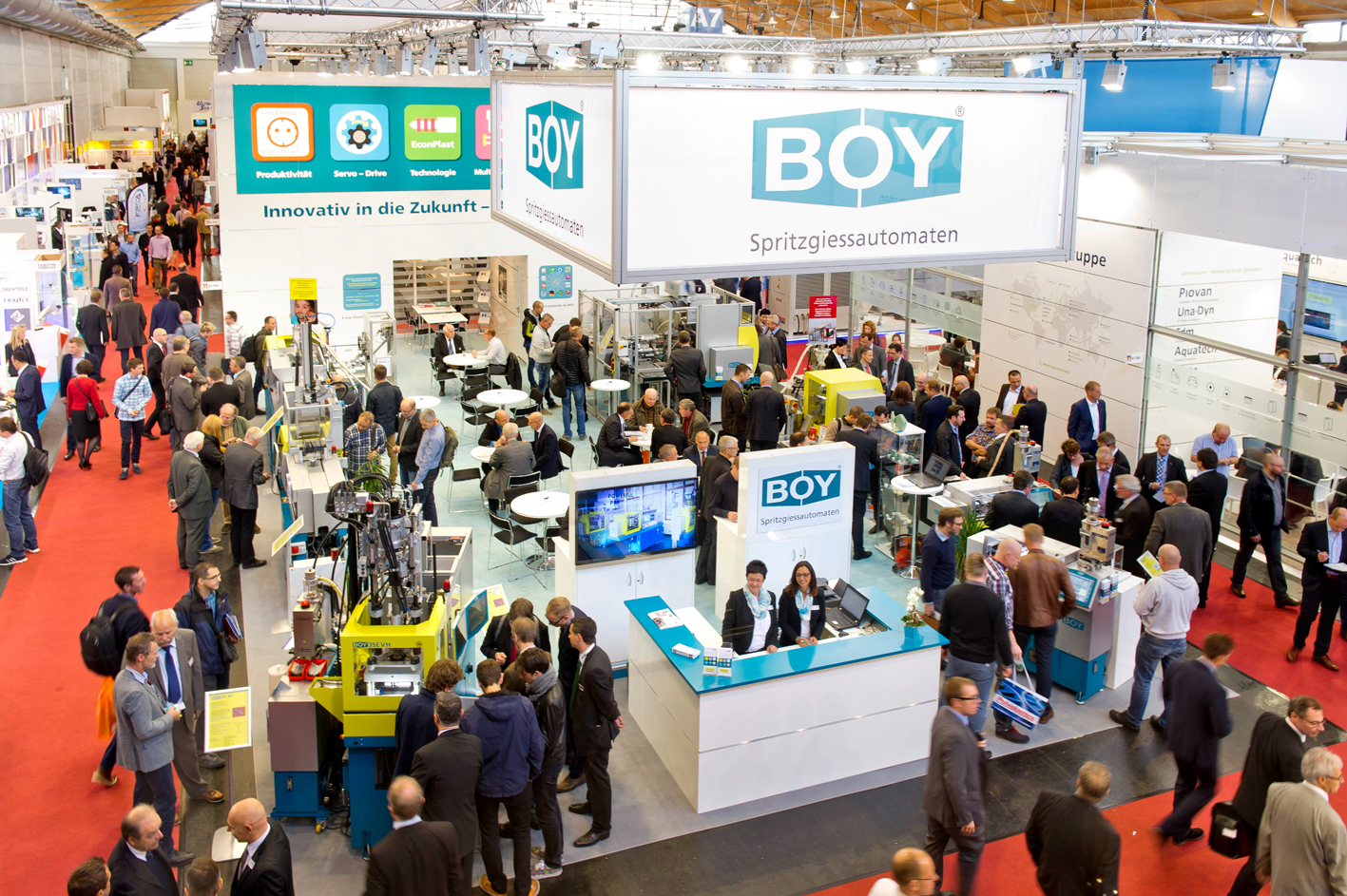 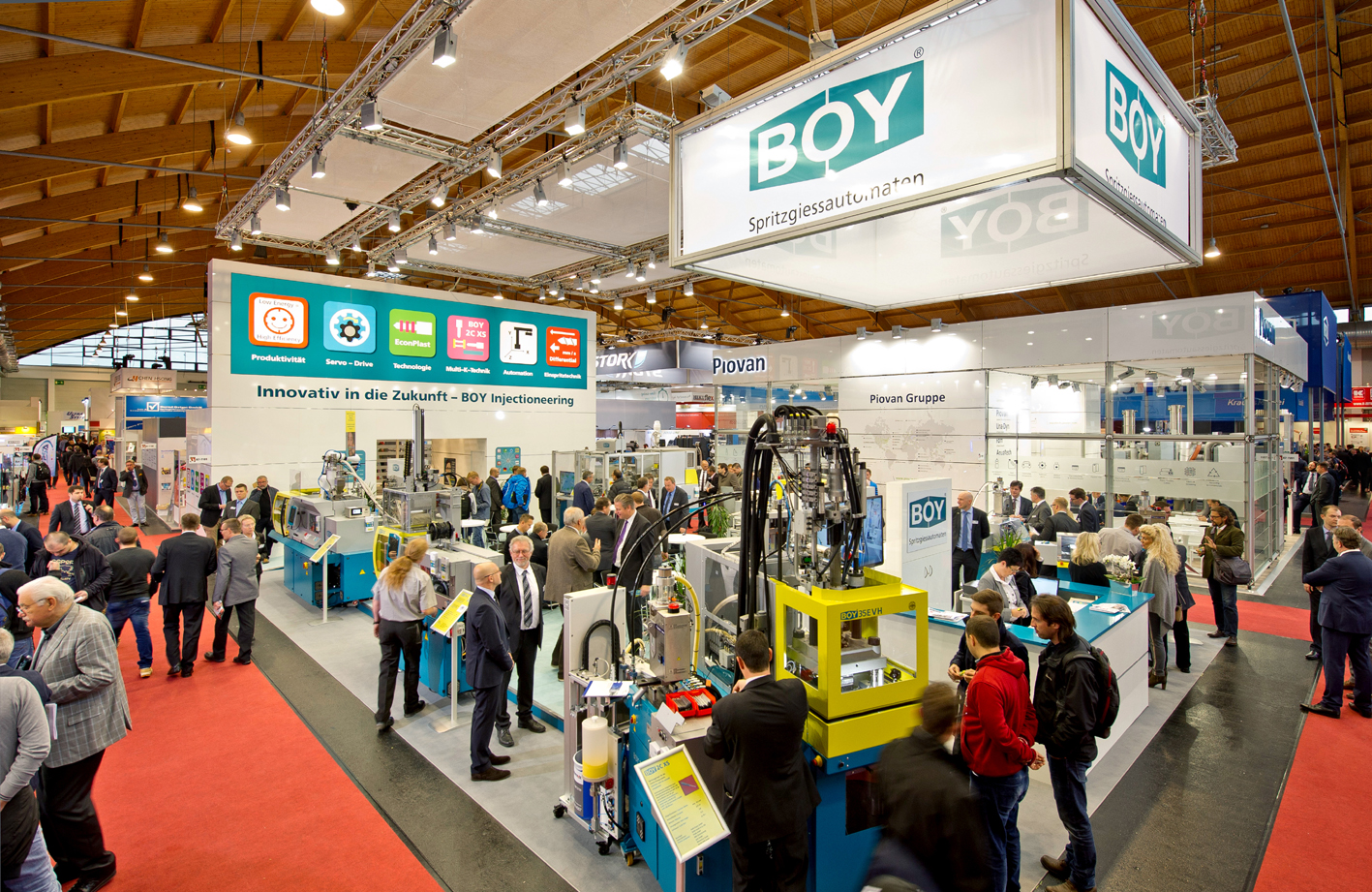
BOY wins large order at Fakuma 2015
BOY noted that during this year´s Fakuma the BOY booth was very well attended from the beginning of the exhibition, promising discussions were held and several orders were placed including a large one.
The visitors were mainly interested in the 3D technology. The individual automation solutions demonstrated on the BOY exhibits and the new, compact 8mm reciprocating-screw plasticizing unit were the other exhibition highlights.
Production of mould inserts using 3D technique
The additive production on customary 3D printers has now also caught the plastics industry. But instead of producing components in 3D technique, the specialist for injection moulding machines with clamping forces up to 1,000 kN decided to go another way. “We produce the mould inserts for our BOY injection moulding machines on a 3D printer“, states Alfred Schiffer, BOY Managing Partner. “With the cost-efficiently produced inserts, prototypes and extremely short runs up to 500 parts can be produced depending on the material. Almost all materials – even glass fiber reinforced plastics – can be processed”. In this way, injection moulded parts can be made that have the same physical properties as conventionally injection moulded parts. This is not possible with the additive component production using 3D printers. A Stratasys-3D-printer in the BOY booth produced the mould inserts in the shortest time, which could be directly installed into the standard mould unit of the BOY XS.
Shorter residence time due to low screw channel volume
The new BOY 8mm reciprocating-screw plasticizing unit celebrated its premiere at Fakuma. The patent pending reciprocating-screw plasticizing unit with only a 8 mm diameter and only a 1,9 cm³ screw channel volume clearly provides a shorter residence time compared to larger screw diameters. This offers clear advantages even when processing thermally sensitive materials. Already existing market solutions with pre-dosing and a 8 mm screw cannot achieve these short residence times. Micro osteosynthesis plates with a part weight of 0,06 g were produced at Fakuma. The residence time of the material in the new plasticizing unit was only 304 seconds.
Better machine equipment for more flexible uses
Six of the seven exhibits in the BOY booth were equipped each with an individually tailored automation solution. “We recognize an increased user interest in complete production units with integrated automation“, states Klaus Geimer, BOY Deputy Managing Director. “On the one hand, we deliver today many more machines which are equipped for the future integration into production lines. On the other hand, handling devices, integrated removal pickers and peripheral devices are also directly ordered. Already ex works, BOY injection moulding machines are increasingly equipped with a multitude of options and accessories. In this way the machines are very flexible to realize the respective automation demand if required. Therefore, our customers are prepared and forward-looking for the Industry 4.0 subject”.
Exhibition result
According to statements of BOY, the medium-sized company from Neustadt-Fernthal is very pleased with the result of this year´s Fakuma. Many promising discussions with prospective customers and new interested persons opened up better chances and possibilities for the future. Due to decreasing batch sizes, the willingness to invest in small, flexible to use injection moulding machines is higher than ever before. The large order given during Fakuma confirms this.
|